引言:AI 大时代,金属新材料长远受益
随着人工智能产业链加速迭代发展,其三大核心要素算法、算力和数据亦有望迈入爆发 式增长。金属新材料作为工业革命发展的基石,亦迎来两大中长期变化:(1) 长期来看,随着算法、算力和数据三大要素逐步突破,未来金属新材料的设计 体系将得以重构,有望加速从理论复杂计算转换至实践应用的产业化,比如高 熵合金、纳米材料等前沿新材料;(2) 中期维度,计算体系升级有望直接带动金属电子新材料需求,比如软磁粉芯、 金属靶材、光模块材料、消费电子(MLCC 镍粉、电极箔、高端铜合金、钽电 容、锡基焊粉材料)、IDC 存储和散热体系等。
长期:三大瓶颈破壁,新材料设计体系优化
大数据时代,新材料开发迈入 AI 阶段
传统新材料的开发往往需要长时间实验积累,其研发时间长达 10-20 年,甚至以上,其 研发和产业化效率相对较低;并且随时新材料的逐步迭代,元素成分愈加复杂且物相变 量增多,传统实验和计算模拟基本已经到达瓶颈阶段,受掣于算法、算力和数据三大掣 肘,新材料产业化节奏有所放缓。未来随着人工智能持续突破,新材料的设计体系有望 加速迈入至大数据计算阶段,带动新材料研发节奏提速和产业化。具体来看,材料科学发展一般可分为四大阶段:(1) 经验测试阶段:早期阶段,新材料研发需要经过长时间的反复试验和应用,开 发周期长且效率较低;(2) 模型理论阶段:在第一阶段基础上,分子动力学和热力学等模型的应用,加速 新材料理论研究走向成熟,提升研发效率;(3) 计算模拟阶段:计算机产业崛起后,计算机迭代仿真模拟计算,进一步提升研 发速度,研发效率大幅提升;(4) 人工智能大数据阶段:通过大数据方式挖掘材料本质要素,并且结合人工智能 和材料研发有效筛选可产业化的高端新材料,缩小筛选范围,并以实验佐证, 新材料发展迈入新阶段。
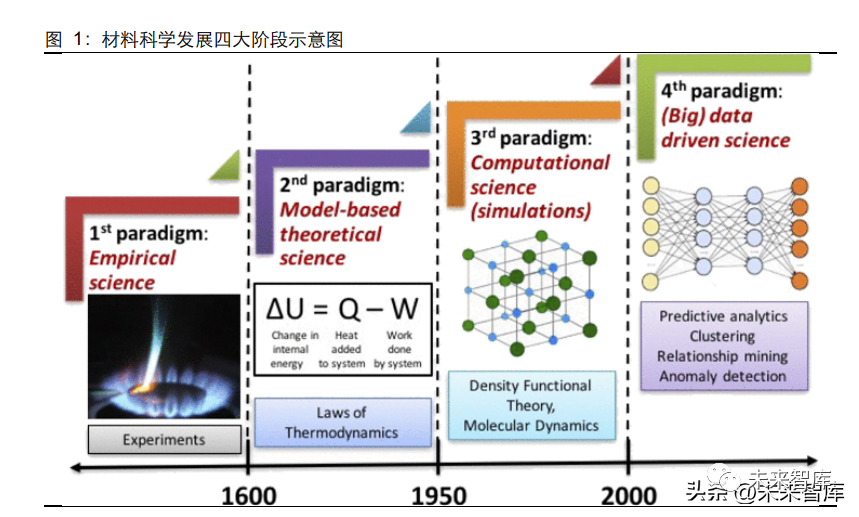
在人工智能大数据阶段,新材料的研发思路是建立工艺、成分、结构、性能之间的内在 联系,根据性能的需求,设计新材料成分和组织的微结构;其次,设计并优化材料成分 与工艺,以实现“材料按需设计”。
材料基因工程,助力新材料研发智能化
我国亦在有效推动新材料开发设计智能化进程,国家重点研发计划“材料基因工程关键 技术与支撑平台”重点专项的实施,是实现“中国制造 2025”的重要内容。材料基因工 程是新材料领域的重大前沿技术,已作为重大战略任务在“新材料重大工程”专项中布 局。根据工业和信息化部产业发展促进中心网,材料基因工程重点专项的主要任务是:按照 全链条创新设计、一体化组织实施的要求,本着融合发展、协同创新的基本理念,围绕 实现两个“一半”的战略目标,构建三大示范平台,研发四大关键技术,开展五类材料 的示范应用。
(1)构建三大示范平台:通过凝聚国内现有的软硬件条件,构筑可融合发展、协同创 新的高通量计算、高通量合成与表征、专用数据库三大示范平台,形成支撑材料基因工 程基础研究的基本软硬件条件和数据体系。(2)研发四大关键技术:针对材料基因工程的关键基础和共性问题,研发多尺度集成 化高通量计算方法与计算软件、高通量材料制备技术、高通量表征与服役行为评价技术、 面向材料基因工程的材料大数据技术,为加速材料创新发展提供技术支撑。(3)典型材料示范应用:在构建三大示范平台和突破四大关键技术的基础上,本着材 料基因工程中计算(理论)/实验(制备和表征)/数据库相互融合、协同创新的研发方式 和理念,选取具有重大战略需求或重大突破意义的高端制造业关键材料,如能源材料、 生物医用材料、稀土功能材料、催化材料、特种合金等,以及材料服役共性技术进行突 破,开展应用示范。
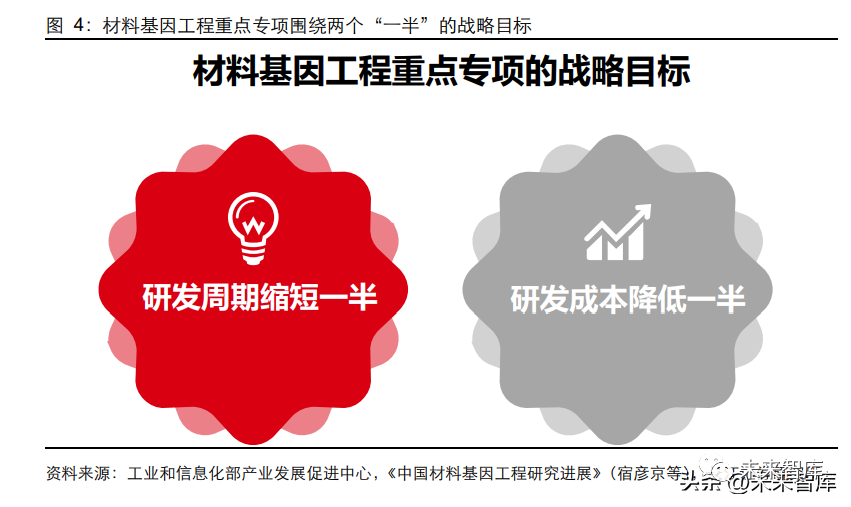
展望:高熵合金、纳米材料,或迎曙光
随着算法、算力和大数据体系愈加完善,先进前沿金属新材料的开发有望在两个维度迎 来突破:(1) 一是成分复杂多元的合金体系,基于每两种、每三种、甚至每四种元素之间容 易形成多种不同的物相,其组合种类繁多,且工艺(温度、时间、压力)进一 步添加多个变量因子,导致材料最终组织和性能种类甚多,传统计算模拟和实 验难以突破,因此在人工智能大时代,这类成分复杂合金的研发有望破壁,比 如高熵合金等;(2) 二是高端纳米材料,纳米材料指结构单元尺寸在 1-100 纳米之间的材料,是处 在原子簇和宏观物体交界的过渡区域,它具有表面效应、小尺寸效应和宏观量 子隧道效应。它的光学、热学、电学、磁学、力学以及化学方面的性质和大块 固体相比显著不同。其往往用量子力学取代传统力学的观点来描述它的行为, 因此其研发设计理论和制造工艺都相对复杂。人工智能技术推动下,纳米材料 的研发和制造效率均有望大幅改善。
高熵合金
高熵合金通常包含 5 种以上的主要元素,各主元的原子分数在 5%~35%之间,主要包 括第 3 周期的 Mg,Al;第 4 周期的 Ti,V,Cr,Mn,Fe,Co,Ni,Cu,Zn;第 5 周期的 Zr,Nb,Mo,Sn; 第 6 周期的 Hf,Ta,W,Pb,另外还有类金属元素 Si,B 等,具有高强度、高硬度、磁特性等 性能,在耐腐蚀、耐高温、耐磨性等方面具有极好的应用效果,可用于焊接材料、储氢 材料、耐蚀材料等的制造。从传统低熵金属到高熵合金,材料综合性价比中枢整体抬升。目前来看,中熵合金和高 熵合金的交界处,是金属材料综合性价比最高区域,例如超合金、非晶合金、不锈钢、 中熵合金等更具成本效益。倘若未来高熵合金随着人工智能而加速成分工艺优化,其成 本有望显著改善,则将打开广阔新材料产业化空间。
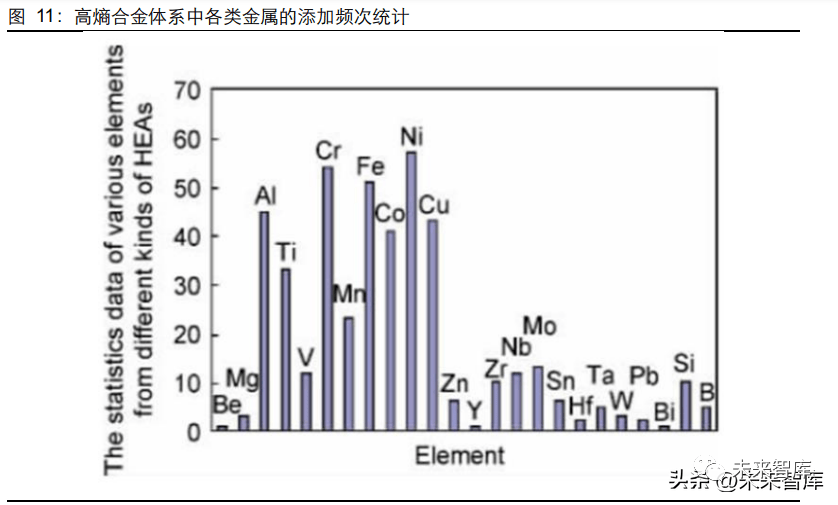
纳米材料
根据北鲲云和中关村在线报道,纳米材料研究,一方面需要高算力,保证并行处理性能。无论是在美国能源部所属的橡树岭国家实验室还是劳伦斯伯克利国家实验室,亦或是国 家能源研究科学计算中心(NERSC),都将旗下部署的超算中心中超过六分之一的机时 用于材料科学相关的研究;另一方面,在计算运行过程中,也会产生大量的过程文件, 若是每天算 1000 个密度泛函理论的材料计算任务,就会产生约 1TB 的数据,对存储系 统要求较高。通过北鲲云超算平台对纳米材料进行计算模拟,可将新材料的发现速度提高 100 倍以 上,纳米新材料研发效率大幅提升。
中期:AI 技术创新驱动,算力、消费电子、数据 产业链多维受益
算力:AI 驱动算力提升需求,GPU 与光模块新材料充 分受益
算力作为人工智能的基础设施,有望迎接全面升级。根据长江计算机,人工智能的发展 一般有三大要素,分别为算力、数据和算法,其中算力是底座,是基础支撑。此次由 ChatGPT 带来的新一代人工智能技术革命,由于其参数量大,在当前的训练阶段和未 来泛在的推理过程中对算力的需求大幅提升,这也符合每一次重大科技变革时期会出现 全新的基础设施这一规律。当前社会有望迈入由人工智能引领和驱动的数字经济时代, 作为底层通用技术或将泛在化和各行业融合,其基础建设重要性凸显。算力的提升依赖于计算芯片的升级,当前主要的计算芯片包括 GPU、NPU、ASIC、FPGA 等,GPU 依然是市场的最为主要的支撑点。GPU 最原始的运用是图形处理器,而随着 GPU 在并行计算方面优势逐步显现,形成了专门以运算功能为主的分支 GPGPU。在人 工智能领域,GPGPU 在云端运行模型训练算法,可以显著缩短海量训练数据的训练时 长,减少能源消耗,进一步降低人工智能的应用成本。与此同时,GPGPU 能够提供完 善的软件生态系统,便于各种已有应用程序的移植和新算法的开发,因此成为全球人工 智能相关处理器的主要解决方案。根据 IDC,2021 年上半年中国人工智能芯片中,GPU 占 90%以上的市场份额。
ChatGPT 浪潮下,计算型 GPU 需求有望高增。当前,我国人工智能领域应用目前处于 技术和需求融合的高速发展阶段,预计 GPGPU(计算型 GPU)市场规模将保持 40% 到 50%的增长,2024 年市场规模有望达到 694 亿元。全球范围来看,根据华经产业研 究院,2027 年全球 GPU 市场规模有望达到 1853 亿美元,2020-2027 年复合增速 33%。
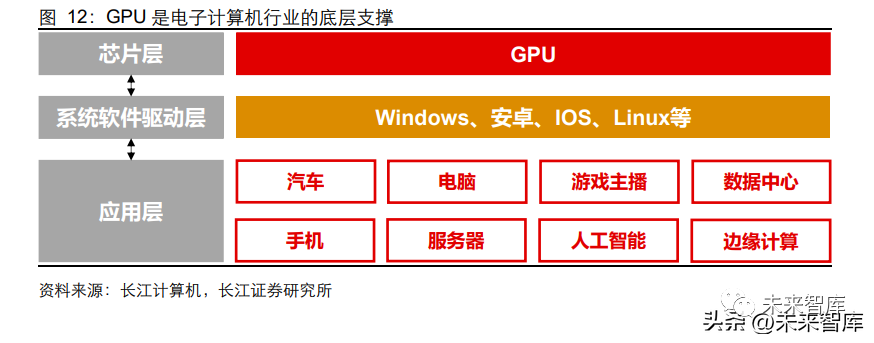
面对持续提升的算力需求,GPGPU 的技术创新如火如荼。展望未来,GPGPU 的技术 创新主要有两个方向,一方面,GPGPU 通过提升工艺制程、增加运算核心数量、采用 更高带宽的片上存储器、提高存储器的带宽和容量等举措,进一步优化芯片的集成度和 性能;另一方面,高带宽、低延时的片间互连总线结构是未来产品优化提升的方向。为满足 AI 对算力提升的需求,英伟达发布 ChatGPT 专用 GPU,在硬件上取得了较大 突破,与上一代产品相比,针对大型模型提供高达 9 倍的 AI 训练速度,印证产品迭代 速度之快。
AI 对算力升级的需求永无止境,然而单个 GPU 算力提升毕竟有限。由此,算力的持续 增强需要多个 GPU 之间协作能力的提升,在每个 GPU 之间实现无缝高速通信的多节 点、多 GPU 系统的需求。速度更快、可扩展性更强的 GPU 互连已成为当前的迫切需 求,光模块产业链有望充分受益。2010 年 6 月,英伟达开始推广 GPU Direct 技术,旨在优化 GPU 之间(P2P)和 GPU 与第三方设备(RDMA)的数据传输。在未使用 GPU Direct 之前,GPU 数据传输需要 复制两次,而通过 GPU 通信实现内存共享后,只需一次内存复制,从而降低数据交换 的延迟。2015 年,英伟达推出 NV Link 技术,进一步加强 GPU 通信效率,当前 NV Link 已经升级至第四代,单个 H100 GPU 支持多达 18 个 NVLink 连接,总带宽为 900GB/s, 助力打造 AI 和高性能计算(HPC)强大的端到端平台。
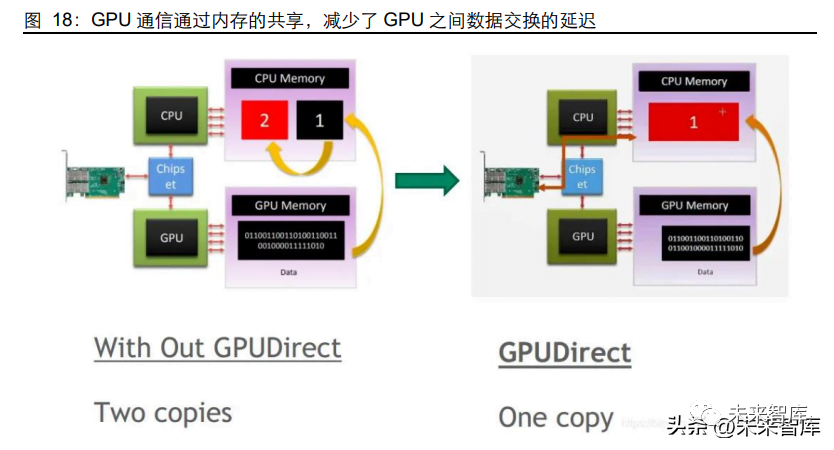
GPU 通信技术需要依靠光模块来实现,AI 兴起催生光模块带来广阔的升级空间。光模 块是一种光电转换器,用于高带宽数据通信应用中,实现光信号和电信号的相互转换。信息网络主要以光纤作为传输介质,但目前计算、分析还必须基于电信号,由此光模块是实现光电转换的核心器件。AI 大模型的广泛训练和应用,有望驱动光模块向更高传输 速率升级。当前,400G 光模块部署正在数据中心网络中加速推进,同时 800G 光模块正蓄势待发, 有望在网络和云服务广泛应用。根据 Yole,2020 年全球光模块市场产生的收入达到约 96 亿美元,预计 2026 年达到 209 亿美元,2020-2026 年的复合增长率为 14%,其中 用于数据的光模块市场有望达到 151 亿美元,2020-2026 年的复合增长率为 19%。AI 兴起对算力提升的需求催生光模块成为更为靓丽的细分赛道。
总结来看,AI 兴起产生的算力提升浪潮下,金属材料产业链有望充分受益:(1)金属软 磁粉末制作的高频降压电感用于 CPU、GPU 供电,与当前主流的铁氧体电感相比,能 节省 50%~75%的空间,且具有散热效果好、低电磁辐射、可靠性高等特点,有望在新 一代 GPGPU 中广泛应用;(2)高纯溅射靶材用于“晶圆制造”和“芯片封装”两个半 导体制造环节,在 GPGPU 集成度提升和小型化发展的趋势下,高纯溅射靶材迎接新的 技术挑战,亦具备广阔的升级机遇;(3)随着光模块传输速率的升级,对光模块基座材 料的高温低膨胀特性和高导热特性提出更高要求,仅高性能的钨铜合金能够满足,有望 充分受益于产业链的升级。
高频降压电感:小型、高频化驱动,金属软磁材料空间广阔
金属软磁材料芯片电感大有可为,有望在新一代 GPU 广泛应用。芯片电感起到为芯片 前端供电的作用,可广泛应用于服务器、通讯电源、GPU、FPGA、电源模组、笔记本 电脑、矿机等领域。目前,主流芯片电感主要采用铁氧体材质,但铁氧体饱和特性较差, 随着未来电源模块的小型化和应用电流的增加,铁氧体电感体积和饱和特性已经很难满 足未来发展趋势,而金属软磁材料电感具有更高效率、小体积、能够响应大电流变化的 优势,有望在百亿级规模市场实现对铁氧体材质电感的全面替代。
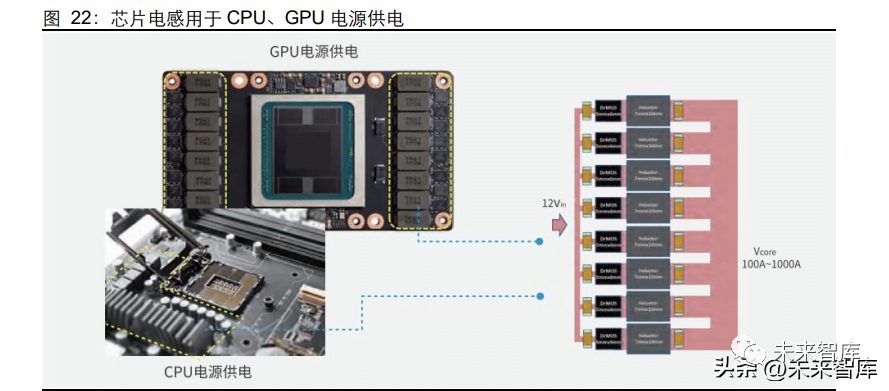
金属粉芯的特点是可以承受大电流、大功率,并且相比于铁氧体电感可以大幅减小体积。根据铂科新材公告,电脑或者服务器主板上面的芯片需要供电才能运算,一般供电电压 不超过 1V,如果电压太高容易击穿芯片,需要芯片电感对电路降压。电压要从 24V 或更 高降低到 1V,电压下降同时电流相应要提升十多倍。传统芯片电感普遍采用铁氧体, 电路需要几级变压,比如从 48V 先降到 24V,再降到 12V,再降至 1V;金属软磁芯片 电感可以直接从 24V 降到 1V。并且,基于金属软磁在饱和磁感应强度上的优势,由最 新一代金属软磁粉芯(NPX)制备的电感在损耗性能上和铁氧体接近,在体积上同比减 少 50%~75%,符合计算芯片高集成、小型化的发展趋势。当前,金属软磁材料芯片电感已经实现交货,目前以服务器领域的应用场景居多,倘若 稳定性符合标准,替代过程有望加速。
高纯金属靶材:计算芯片迭代加速,高纯金属与靶材需求高增
高纯溅射靶材是半导体、平板显示器、太阳能电池等领域生产所需的关键材料之一,是 具有高附加值的功能性材料。由于该行业的技术门槛、资金门槛和人才门槛较高,我国 仅有极少量的本土企业能够成功进入全球知名半导体芯片制造商、平板显示器制造商的 供应链体系,为其批量供应靶材产品。高纯溅射靶材的应用领域中,半导体领域对于溅射靶材的技术要求最高,其对于金属材 料纯度、内部微观结构等均有严苛的标准。半导体芯片制作过程分为硅片制造、晶圆制 造和芯片封装三大环节,而高纯溅射靶材主要用于“晶圆制造”和“芯片封装”两个环 节。在晶圆制造环节被用作晶圆导电层、阻挡层以及金属栅极的溅镀,在芯片封装环节 被用作贴片焊线的镀膜。在半导体领域,一般选用高纯铝靶、钛靶、钽靶,对金属的纯 度要求达到 6N(99.9999%);长期以来,以日本、美国为代表的溅射靶材生产商在掌 握核心技术以后,执行严格的保密和专利授权措施,对于新进入者设定了较高的技术门 槛,使得当前半导体靶材国产化率处于较低水平。展望来看,AI 赋能计算芯片迭代加速+政策的大力支持+国内企业技术、资金和人才门槛 逐步突破,有望为高纯金属和高纯靶材带来靓丽的增长空间,使之成为复合增速 15%+ 的高增长赛道。
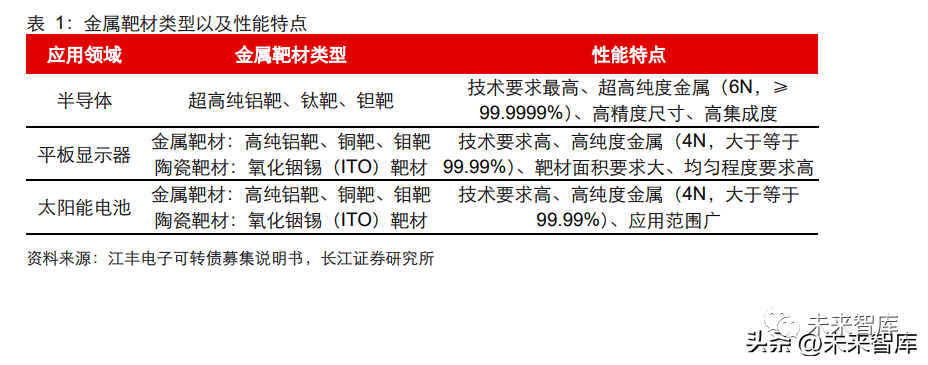
钨铜合金:光模块传输速率升级,高性能钨铜合金蓄势待发
光模块由光器件、功能电路和光接口组成。主要功能为完成光信号的光电、电光转换。主要用于电信传输、数据中心和 5G 基站。模块中有件三大核心部,光芯片、激光器和 光棱镜;此三大部件对载体材料的散热系数和热膨胀系数有着苛刻的要求,此载体叫光 芯片基座。随着光模块传输速率的升级,钨铜合金成为光芯片基座的必备材料。根据斯瑞新材公告, 能满足 100G 以上速率光模块性能要求的基座材料只有可伐合金(Kovar)和钨铜合金 (CuW)、钼铜(CuMo)。200G/400G 光模块使用 CuW 光芯片基座来保证散热。CuW 合金既有钨的低膨胀特性,又具有铜的高导热特性,其热膨胀系数和导电导热性可以通 过调整材料的成分而加以改变,以使之与芯片的热膨胀系数更匹配。由此,钨铜合金或 将成为 800G 光模块架构下,光芯片基座成熟的解决方案。国内钨铜合金生产企业正逐步打开光芯片基座市场。当前,国内铜合金生产企业中,以 斯瑞新材为代表的企业所生产的钨铜合金正在逐步通过下游标杆客户认证,进入国际供 应体系,目前潜在的直接客户有菲尼萨(Finisar)、AOI、中际旭创、天孚通讯、新易盛 等。从斯瑞新材官网上可看到,公司的钨铜合金光模块基座材料已经应用于全球最大、 技术最先进的光通讯器件供应商菲尼萨的产品。
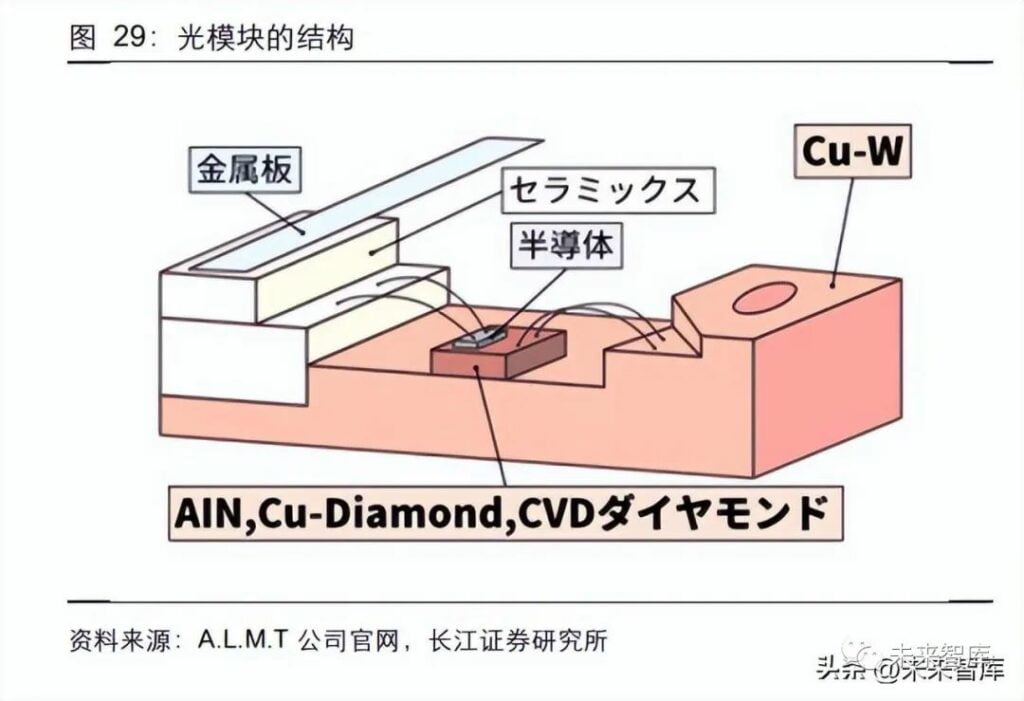
消费电子:AI 技术创新,有望引领消费电子新一轮景气
复盘来看,消费电子每一轮景气周期,都由技术创新所驱动。如 11-14 年的智能手机崛 起、15-17 年智能手机的高端化升级、18 年至今的 VR/AR,汽车电子等。而随着 AI 在 重大技术创新的突破,有望引领新一轮消费电子景气浪潮,消费电子上游金属新材料环 节有望充分受益。
MLCC 镍粉:景气拐点渐临、纳米镍粉显著受益
MLCC 是电路中广泛应用的电容器之一,目前电子产品的多功能化和便携式的发展趋势 要求电子元器件产品在保持原有性能的基础上不断缩小尺寸。因此,MLCC 不断在向薄 层化、小型化方向发展,MLCC 用镍粉粒径也不断缩小,近几年使用的镍粉粒径从 600nm、 400nm 向 300nm、200nm 及其以下靠近。博迁新材采用常压下物理气相冷凝法(PVD)制备超细金属粉末,填补了国内该技术产 业化的空白,并且公司作为唯一起草单位,起草与制定了我国第一项电容器电极镍粉行 业标准,是目前全球领先的实现纳米级电子专用高端金属粉体材料规模化量产及商业销 售企业。凭借优质的技术工艺和成本管理等竞争力,公司打破全球 MLCC 用镍粉垄断市 场,进入全球市占率超过 20%的 MLCC 巨头三星电机的供应体系当中,成为其重要供 货商。三星电机不仅实现了电介质用核心粉末的世界最小粒子 50nm,同时也拥有世界 领先的小型化和叠层的技术能力,叠加博迁作为三星的供货商,为三星提供了世界先进 的微小粒径镍粉。
展望来看,博迁新材将研发下一代 50nm 和 30nm 的 MLCC 用纳米镍粉;扩大现有产 能,巩固市场地位;新建一条 HJT 异质结电池用银包铜粉中试产线,持续推进产品稳定 性测试,深入挖掘规模化生产降本增效潜力,为后续银包铜粉规模化量产提供有效技术 支撑;推动锂电池负极材料用纳米硅粉生产过程持续的工艺优化;推进银包铜粉与纳米 硅粉的研发,将为公司后续发展提供长足动力。
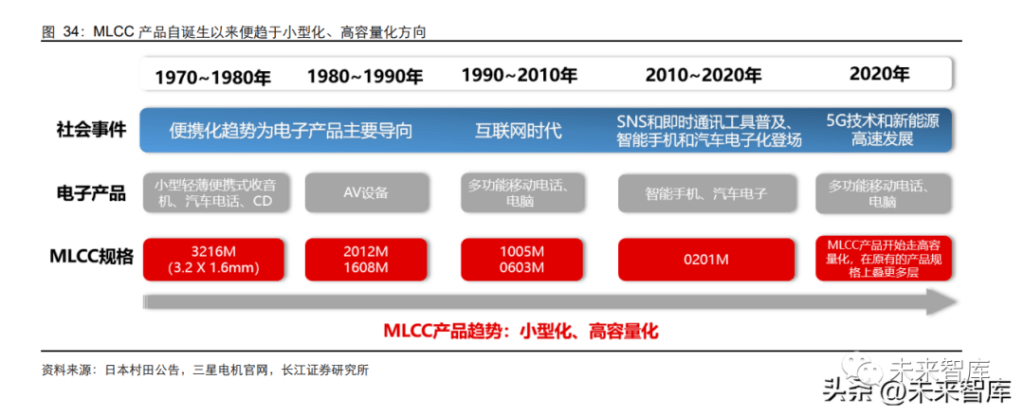
铝电极箔:消费电子与新能源叠加,需求稳步提升
铝电极箔为生产铝电解电容器的主要材料,电子铝箔与电解液的生产成本占铝电解电容 器总成本的 30%至 70%(随电容器大小不同而有差异)。铝电解电容器作为最基本的电 子元件之一,被广泛用于电子信息行业以及家电等各类电子产品之中,具有体积小、电 容量大及成本低的特性,尤其是单位电容量价格在所有电容器中最为便宜,符合信息产 品低价化发展趋势,市场需求量极大。下游终端领域中,铝电解电容器最主要应用领域是消费电子,占比达到 45%,其次电脑 及周边产品占比 24%,节能照明占比 14%。新能源行业普遍需要变频以将电力输送至 电网,因此风电、光伏中也广泛应用铝电解电容器。
竞争格局上,高纯铝、电子铝箔、电极箔的行业集中度依次降低。高纯铝、电子铝箔需 规模化生产才能具有生产效益,且技术壁垒、资本壁垒较高,行业集中度高,目前仅新 疆众和、包头铝业、天山铝业等少数几家企业可以大规模生产高纯铝,仅新疆众和、东 阳光具备大规模生产、稳定供应电子铝箔的能力。全球电极箔的生产企业众多,除十几家规模较大的企业外,其余均为中小企业,市场竞 争较为激烈。其中日本 JCC 公司技术相对领先,国内产能较大的主要厂商包括东阳光、 新疆众和、海星股份等上市公司,部分电容器厂商为保障自身原材料供应,也正在发展 电极箔业务。
特殊铜合金:消费电子企稳复苏,汽车电子空间广阔
过往来看,传统铜材增速缓慢;当下,新能源和新基建的兴起,为高端的特殊铜合金材 料打开广阔的增量空间,以汽车电子、消费电子、通讯电子为主要下游的高端铜箔材、 铜带材成长性更佳。横向对比看,2021 年我国铜箔材、铜板带材产量同比增长 31.9%、15.7%,远高于整体 铜材 4.9%的平均增速,映射新能源、新基建需求下的增长弹性;纵向对比看,2020 年, 我国铜箔材、铜带材的增速为 6.8%、5.3%,2021 年增速较 2020 年大幅提升,表明此 轮需求或刚刚兴起,未来成长空间值得期待。
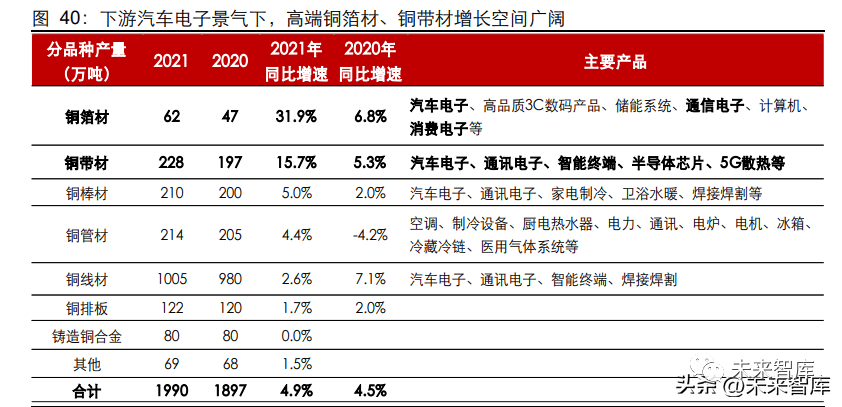
我国铜材产量虽居世界首位,但铜合金材料产业却大而不精,行业利润难以支撑高新技 术研发,相关企业的新材料研发能力不足,部分高端铜材仍依赖进口。从进出口数据看, 我国进口铜材平均价格高于出口铜材平均价格30%以上,进口铜材数量约50万吨(2019 年),印证我国在高端铜材上仍有较大进口替代空间。
新能源汽车景气+AI 为汽车电子赋能,为高端铜合金材料带来广阔需求空间。单车用铜 量上看,纯电动汽车用铜量接近传统汽油车的 4 倍,混合动力车用铜量接近传统汽油车 的 2 倍。据测算,传统燃油车单车用铜量为最多可达 22kg,而混合动力车、纯电动汽 车单车用铜量分别可达 40kg,83kg。而在 AI 大时代下,汽车有望在智能化、网联化、 电气化、共享化实现进一步跨越,带动单车耗铜量的提升。
铜合金材料机械性能中,最重要的是强度和导电性能。当下消费电子和汽车电子的发展, 对铜合金材料的强度和导电性能提出更高要求。当前博威合金在特殊铜合金材料的研发 上处于领先地位,通过对生产工艺的革新以及合金材料的不断改善,从“固溶+形变” 的第一代强化型合金更新升级到第三代析出强化型合金,在追求高强、高导的同时,还 具有优异的折弯和抗应力松弛性能,充分满足消费电子和汽车电子的升级需求。
钽电容、钽靶材:AI 赋能,高端电子材料前景广阔
钽具有熔点高、蒸汽压低、冷加工性能好、化学稳定性高、抗液态金属腐蚀能力强、表 面氧化膜介电常数大等一系列优异性能,在电子、冶金、钢铁、化工、硬质合金、原子 能、超导技术、汽车电子、航空航天、医疗卫生和科学研究等高新技术领域有重要应用。电子领域在钽下游需求结构约占一半左右。钽的下游需求结构中,钽电容器和钽溅射靶 材分别占比 34%和 15%,二者合计约占钽半数需求,由此钽的需求和电子行业景气度 具有较高的一致性。此外,钽的化学品以及超级合金占比分别为 17%和 18%。
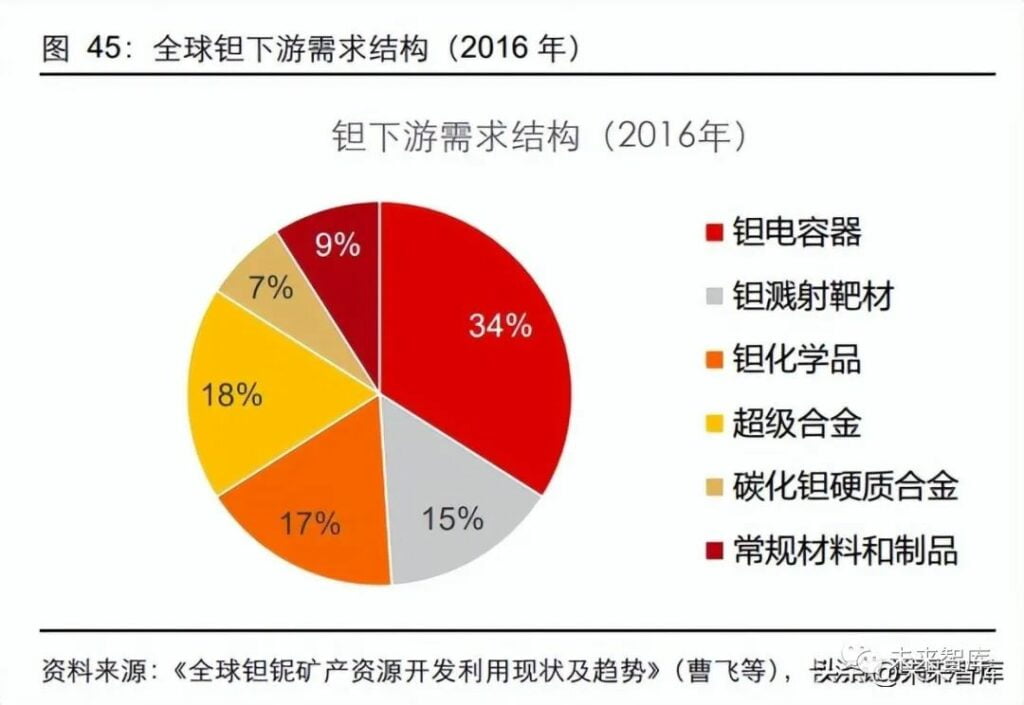
钽电容器作为高端电容器材料,主要应用于高可靠性军用和高端民用电子设备。钽以电 容器级钽粉和钽丝的形式用于制作钽电容器。由于钽的表面能形成致密稳定、介电强度 高的无定形氧化膜,易于准确方便地控制电容器的阳极氧化工艺,同时钽粉烧结块可以在很小的体积内获得很大的表面积,因此钽电容器具有电容量高、漏电流小、等效串联 电阻低、高低温特性好、使用寿命长、综合性能优异等优点。然而,相对于当前广泛使 用的陶瓷电容器和铝电解电容器,钽电容器成本较高,主要应用于高可靠性军工电子设 备,以及 5G 等高端民品市场。
AI 赋能下,钽电容、钽靶材等高端电子材料应用前景或更为广阔。基于钽电容器主要应 用于高端市场,过往行业增速相对缓慢,市场占有率呈逐步下降的趋势。2015-2020 年, 国内钽电容器市场规模的复合增速为 2.8%,对比行业的复合增速为 5.6%。2020 年, 国内钽电容器约占电容器市场规模的 5%(按产值计算),而成本相对更低的陶瓷电容器 和铝电解电容器的市占率分别占 53%和 26%。钽电容器使用金属钽作为介质,而其他电容器使用电解液为介质,由此钽电容器耐高温 的性能更为优异,特别适用于温度范围比较宽的应用场景。在 AI 兴起驱动的功耗升级 下,电子材料发热量显著增加,催生对耐高温电容器的广阔需求空间。钽靶材主要用于智能手机、平板电脑等消费电子产品,过往高纯钽靶材价格昂贵,主要 用于高端芯片,有望充分受益于 AI 驱动的半导体产业链升级浪潮。
锡基焊粉材料:电子领域需求占比 85%,充分受益电子景气复苏
锡具有质地柔软、熔点低、延展性好、易与许多金属形成合金、无毒和耐腐蚀等特性, 是最具广泛工业用途的金属之一,主要用于制造锡焊料、锡化工制品、镀锡板、浮法玻 璃、锡合金等。微电子锡基焊粉材料具体应用领域包括以印刷电路板为载体的各类电子 模块和电子产品的制造,我国锡焊料产量约占全球产量的 65%,是全球最大的锡基焊粉 生产国。锡的下游消费结构中,包括电子、食品、化工、轻工、医药等传统行业,其中电子行业 是最重要的下游行业。锡焊料作为锡下游主要产品,在锡的消费结构占比 49%,而电子 领域在锡焊料占比占 85%。由此,锡价与集成电路产量增速高度相关。而新能源领域需 求的兴起,在汽车、能源行业为锡金属带来广阔的增量空间。
微电子锡基焊粉材料行业在市场空间、应用领域、技术演进和产品革新等多方面都因下 游行业应用需求增长和升级的驱动而发展。微电子锡基焊粉材料由于其高可靠、高性能 的特点,是电子组装必不可少的材料,广泛用于电子制造业的半导体封装、电子元器件 装配等。随着电子产品的小型化、微型化、轻量化发展,微电子锡基焊粉材料行业处于 在合金成分上向无铅化、低温化等方向发展;在性价比上向高可靠、低成本方向发展;在产品尺寸上向微细化、窄粒度方向发展;产品应用上逐渐向功能化、低温节能方向发 展。整体而言,高端微电子锡基焊粉材料市场空间正在逐步打开。
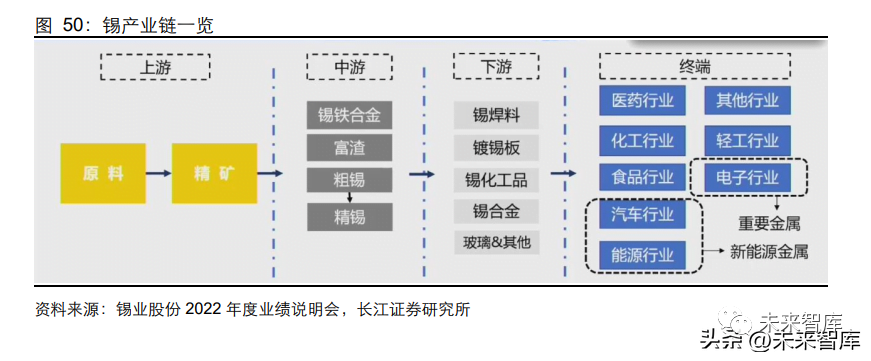
竞争格局上看,目前微电子锡基焊粉材料国外企业包括德国贺利氏、美国爱法、日本千 住、法国意普斯,国内企业包括有研粉材、升贸科技、锡业锡材等企业。其中,美国爱 法、日本千住、升贸科技生产的锡基焊粉材料以自用为主。据中国电子材料行业协会电 子锡焊料材料分会统计,其会员单位的锡焊粉产量可覆盖全国产量 80%以上。有研粉材 的国内市占率超过 15%,总产量、销售量及市场占有率均为国内第一(2019 年)。
除加工端外,在 AI 大时代下,锡产业链原料端的景气亦值得重视。除电子领域新一轮 上行周期对锡需求的提升作用之外,光伏领域有望打开锡的新的需求空间。光伏领域中 光伏组件连接需要焊锡将光伏焊带连接以进一步提升转换效率。近年来在能源转型过程 中光伏产业快速发展,光伏焊带用锡需求保持高速增长,成为促进锡消费在新能源领域 较为稳定的增长亮点。根据立鼎产业研究院,目前光伏焊带以镀(涂)锡铜带为主,锡含量约为 17%;光伏组件焊带的使用量在 550~800 吨/GW,其中镀层(涂层)的锡含 量在 60%或 63%(对应不同焊带类型),因此光伏用锡量约为 56~86 吨/GW,取中值在 70 吨/GW 左右。根据长江电新,预计 2025 年全球光伏新增装机容量将达到 585.1GW, 对应约 4.1 万吨锡焊料需求,2022 到 2025 年复合增速为 33%。整体来看,2025 年,在电子、光伏双轮驱动下,预计全球锡需求为 43.84 万吨,22-25 年复合增速为 4.9%,锡资源端企业有望充分受益。
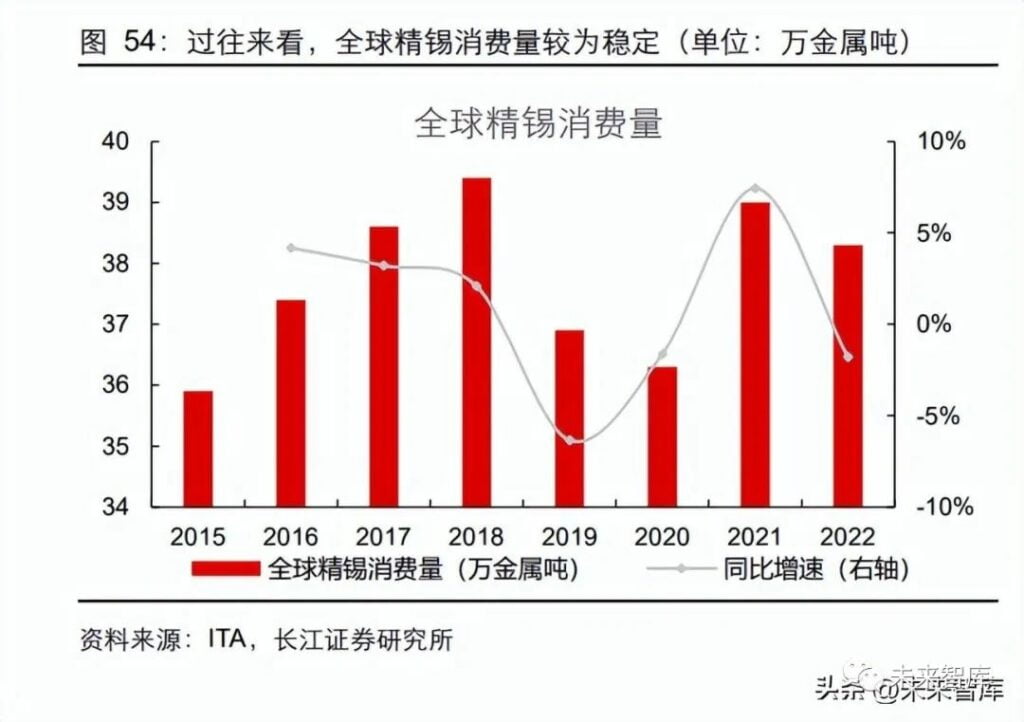
测算依据如下依据和假设:1) 根据 ITA,2022 年全球消费金属锡 37.95 万吨,其中锡焊料、锡化工、镀锡板、铅 酸电池、锡铜合金、其他领域分别占比 49%、17%、12%、7%、7%、8%。2) 根据 ITA,2018 年全球锡焊料下游应用分为消费电子、通信、计算机、汽车电子、 工业及其他用途,其中电子领域占比 85%,工业及其他用途占比 15%,假设 2022 年这一比例保持不变;3) 根据长江电新,预计 2025 年全球新增光伏装机量 585.1GW,22~25 年 CAGR 为 33%。4) 根据立鼎产业研究院,光伏焊带以镀(涂)锡铜带为主,锡含量约为 17%,光伏用 锡量约在 70 吨/GW 左右,由此测算 2025 年光伏用锡需求 4.10 万吨。5) 根据 ITA 预测,2020~2025 年,电子行业对锡的需求增速约为 5%,工业及其他领 域对锡的需求增速为 6%;假设 2022~2025 年电子、工业领域对锡的需求以 5%、 6%的增速增长。6) 假设化工领域、镀锡板、其他领域对锡的需求 2023~2025 年同比+3%/+2%/+1%, 假设铅酸电池和锡铜合金对锡的需求保持不变。
供给端上看,全球锡储量分布较为集中。据 USGS 数据,2021 年全球锡储量约 490 万 吨,其中,中国锡储量位居全球第一,占比 23%;储量第二至第五位依次为印度尼西亚、 缅甸、澳大利亚和巴西,分别占比 16%、14%、11%、9%。主流供应国家品位下降,催生锡日趋供给紧缺格局。全球主要锡生产国如秘鲁、刚果(金)、 中国、印尼等国经过长年开采,截至 2021 年底,锡储采比分别为 7、8、13、15 年, 已远低于全球平均水平 17 年,尽管近年来探矿活动不断进行,但并未刺激储量明显增 加,锡资源紧缺程度日益加剧。且近年来受宏观环境及区域冲突的影响,行业资本投入 长期不足,目前在投产的新项目短期内达产的可能性较低,短中期内矿端难现放量增长。由此,在需求稳步增长,而供给较为刚性下,锡价中枢有望上移,资源端有望充分受益。
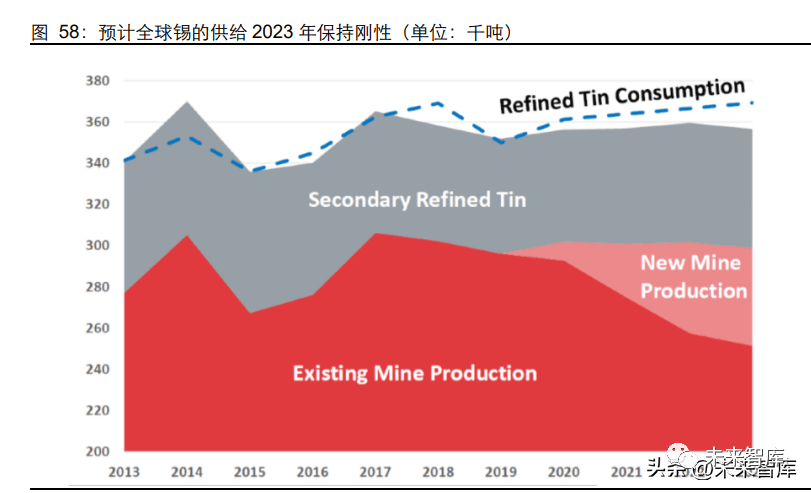
数据:智算时代序幕拉开,IDC 存储和散热体系迎接新 机遇
当前,智算时代的序幕已经拉开。智慧计算融入到千行万业的图景,正在徐徐铺开。这 是一个数据成为生产要素的时代,智慧计算将劳动者由人变成了人+AI,将数据变成了 一种新的生产资料,将计算力驱动的信息化设备变成了生产工具。以 AI 计算为例。自 2012 年以来,AI 算力需求总增长约 30 万倍,即 3~4 月翻一倍(相 比之下,摩尔定律约每两年翻倍,总增长约 7 倍)。在如此高的性能需求下,无论云计 算,还是边缘计算,都已经或将要和私有云或者数据中心的业务系统打通,实现数据的 处理、流动和共享,为全产业链联动,提供及时交付和响应。由此,为 IDC 存储以及配 套的散热体系带来新机遇。
IDC 存储:钢企布局具有先天优势,有望打开第二增长极
IDC 是基于 Internet 网络,为集中式收集、存储、处理和发送数据的设备提供运行维护 的设施基地并提供相关的服务。IDC 提供的主要业务包括主机托管(机位、机架、机房 出租)、资源出租(如虚拟主机业务、数据存储服务)、系统维护(系统配置、数据备份、 故障排除服务)、管理服务(如带宽管理、流量分析、负载均衡、入侵检测、系统漏洞诊 断),以及其他支撑、运行服务等。
对于钢铁行业,布局 IDC 业务具有先天的优势。IDC 是典型资本密集型与资源密集型行 业,被称为“数字地产”,能耗、土地、资金是建成 IDC 的关键三要素。
1) 能耗方面,电力是 IDC 成本的最大组成部分,占 40%~50%。以 PUE1.4、5KW 标准机柜功率计算,一万台机柜能耗 70MW,一年耗电约 6 亿千瓦时。钢企供水 供电厂房等配套到位,可节省相应初期建设成本。多数钢厂拥有自发电系统,相较 外购电成本较低。2) 土地方面,IDC 单机柜占地面积大,各项目间存在差异,根据宝信宝之云四期项目 估计,一万台机柜占地约 4~5 万平方米,折合约 60-80 亩;钢企通常厂区面积大, 且部分钢企拥有搬迁后的闲置厂房,可以低成本改建成 IDC 机房。3) 资金方面,单机柜建设成本在 12~15 万元(5KW 标准机柜功率),建设一万台机 柜就需要十亿元级别的投入。部分钢企目前账上现金储备充裕,整体资产负债率 处于较低水平,资金方面受限较小。
IDC 散热材料:液冷或成为主流方案,铜铝散热材料相对受益
数据中心作为海量数据的主要存储与运算处理实体,其规模不断扩大,能耗问题成为关 键问题。在数据中心能耗占比中制冷系统的能耗占比为 30~40%,是总能耗中占比最高 的数据中心基础设施模块,因此改进数据中心制冷等基础设施技术,提高制冷效率,减 少制冷系统的能耗水平,成为未来重要发展方向。传统的风冷技术无法满足数据中心日益增长的散热需求,液冷在 IDC 领域应用空间广 阔。随着数字经济的持续发展,5G、人工智能等新技术的应用,以及各行业的数字化转 型,数据量爆发增长,要求数据中心向高密度的方向发展,根据《绿色数据中心白皮书》 指出的不同密度数据中心对应的制冷方式,传统的风冷方式只能满足 2.7kW/机柜的数 据中心散热需求,已经无法完全满足数据中心日益增长的散热需求。而液体传导热能效 果和大比热容能够保障 CPU 在一定范围内进行超频工作不会出现过热故障,同时液冷 数据中心省却空调系统和相应基础设施的建设,节省了大量空间,可以容纳更多的服务 器。此外,液冷还具有节能、降噪,无视海拔和地域的差异等优点。
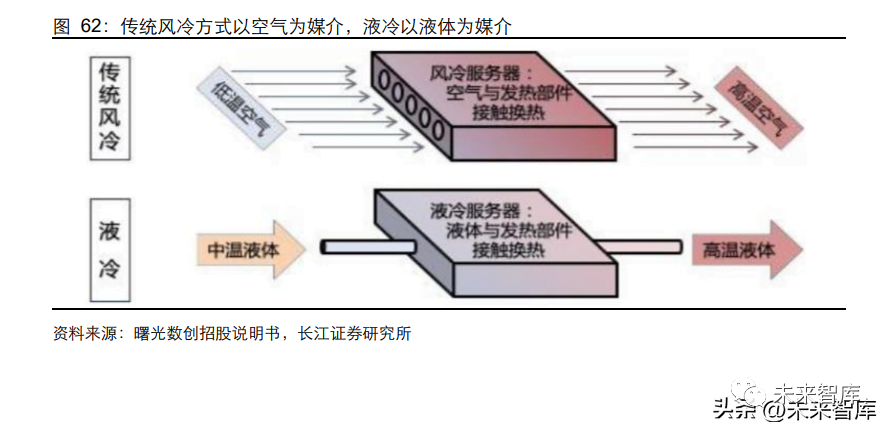
当前,华为、浪潮、联想和阿里等企业在液冷领域不断探索,推动液冷数据中心基础设 施商业化的进程。随着液冷技术逐步成熟与产业化,有望打开广阔的市场空间。根据赛 迪顾问,2019 年我国液冷数据中心市场规模为 261 亿元,预计 2025 年可达到 1283.2 亿元以上。根据赛迪顾问和中国信通院的数据推算,2019 年中国液冷数据中心基础设 施市场规模为 64.7 亿元,预计 2025 年可达到 245 亿元以上。
板式液冷技术通过冷板(通常是铜、铝等高导热金属构成的封闭腔体)将发热元器件的 热量间接传递给封闭在循环管路中的冷却液体,通过冷却液体将热量带走的一种实现方 式。一般采取铝基板内嵌铜制热管形式,热量通过盖板传递到冷板上。随着冷板式液冷 方案的广泛使用,铜铝等散热材料有望迎来广阔的需求空间。
[出处 – 微信公众号 粉末冶金及硬质合金展] 金属新材料行业专题研究:AI大时代,金属新材料投资专题 https://mp.weixin.qq.com/s/6-V7NSXEcztRdYYeHyO8vw